Abstract:
Longitudinal hot tearing, popularly called as end cracking, frequently takes place in the end portions of large steel panels’ butt joints, using one-sided, submerged-arc welding with flux copper backing welding process (FCB welding). The study was to look for the possibility to improve and/or prevent the end cracking issue during FCB welding, center blind-hole drilling technique was used to measure the welding residual stress for five different cases, considering hot tearing mechanism, its influence factors and the relevant reported prevention measures. Unpredictable result was observed subsequently that transverse compressive stress is found on the shallow surface of weld seams, which could give supplementary information to the common assumption for conventional low heat input welding method that cracks initiation is caused by tensile stresses across the welded joints. The study concluded that FCB welding end cracking issue is caused by the comprehensive function of different stresses, and also properly use tack welding practice, suitable elastic run-off plate and relatively low heat input energy which will reduce the end cracking susceptibility for the tested materials.
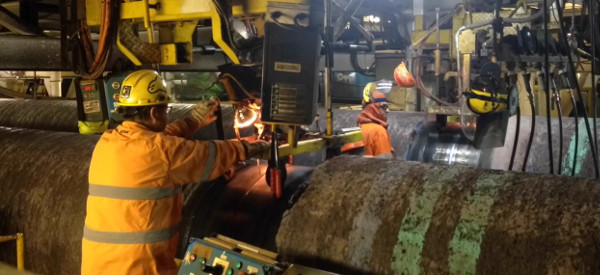
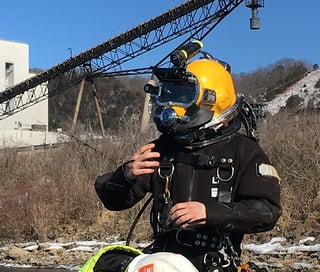
- 👉 Submerged Arc welding. 👉 Ultrasonic Welding 🌟 The powerpoint presentation used for the videos in the form of the PDF file can be downloaded by using the link.
- Submerged-arc welding (SAW) is an arc welding process. It is especially suited for plate thicknesses between two and 100 millimeters. SAW is typically used in the heavy metal industry. Submerged-arc welding: the technology.
[1] CB/Z 278, One-side submerged arc welding process with multiple wires for FCB (In Chinese), (2011).
The invention provides a method for welding a specially-thick high-strength bridge steel plate and belongs to the technical field of specially-thick plate welding. The test plate of the method adopts a symmetric narrow gap U-shaped groove form, is combinedly welded by using two efficient welding methods, namely gas shielded welding for priming.
[2] Yasuhisa Okumoto and Osamu Baba: Improvement of Flux-Copper Backing Welding Quality [J], Journal of Ship Production, Vol. 19, No. 4 (November 2003), pp.223-229.
[3] Tang Muyao, Rui Shuxiang, Xin Dingqian: Study on End Cracking during One-side Submerged Arc Welding, Transactions of the China Welding Instituion, Vol. 7, No. 3 (September 1986), pp.123-132.
DOI: 10.1080/09507118709451094
[4] E L Makarov , H Herold , M Schtraitenberg & A Pshennikov: Preventing hot cracking in end sections of long welds in one-sided, multi-arc, submerged-arc welding, Welding International, Vol. 14, No. 4 (2002), pp.305-309.
DOI: 10.1080/09507110009549184
[5] Okuda, N.: Studies on Generation Mechanism and the Prevention for End Cracking of One Side Automatic Welding Joint, report of Japan Welding Society, welding metallurgy workshop (In Japanese, 1978).
[6] IACS Unified Requirement W11, International Association of Classification Society Ltd. (2013).
[7] Rao Yizhong: Solutions to end cracking issue for FCB weld seams, Academic Conference on Energy conversation and pollution reduction in Shipbuilding Industry, Academic Committee for Naval Architecture, China's Society of Naval Architecture and Marine Engineering (In Chinese), pp.128-132 (2009).
[8] Bengt Akesson and Lennart Larlsson: Prevention of Hot Cracking of Butt Welds in Steel Panels by Controlled Additional Heating of the Panels, Paper D, PhD Thesis, Division of Solid Mechanics, Chalmers University of Technology, Gothenburg, Sweden (November 1973, August 1974, and March 1976).
[9] Zhang Wenyue: Fundamental of Welding Metallurgy, China Machine Press (In Chinese), pp.227-229 (1999).
[10] Dieter Radaj: Heat effects of welding; temperature field, residual stress, distortion. Xiong Dijing etc., Beijing: China Machine Press (In Chinese), pp.210-212 (1992).
DOI: 10.1007/978-3-642-48640-1_3
[11] T Koseki: Solidification and solidification structure control of weld metals, Welding International, Vol. 16, No. 5, pp.347-365 (2002).
DOI: 10.1080/09507110209549544
[12] Cui, Zhong Qi: Metallography and Heat Treatment, Harbin Institute of Technology (In Chinese), pp.296-297 (2000).
[13] Kou S: Welding Metallurgy, Second edition, Publ Wiley-Interscience Corp. pp.285-295 (2002).
[14] S Katayama: Solidification phenomena of weld metals (1st report). Characteristic solidification morphologies, microstructures and solidification theory, Welding International, Vol. 14, No. 12, pp.939-951 (2000).
DOI: 10.1080/09507110009549297
[15] S Katayama: Solidification phenomena of weld metals. Solidification cracking mechanism and cracking susceptibility (3rd report), Welding International, Vol. 15, No. 8, pp.627-636 (2001).
DOI: 10.1080/09507110109549415
[16] Kenji Shinozaki , Yamamoto Motomichi , Wen Peng & Tamura Tomoko: Prediction of occurrence of solidification cracking in weld metal [J], Welding International, Vol. 24, No. 12, pp.942-948 (2010).
DOI: 10.1080/09507111003655325
Abstract:
Longitudinal hot tearing, popularly called as end cracking, frequently takes place in the end portions of large steel panels’ butt joints, using one-sided, submerged-arc welding with flux copper backing welding process (FCB welding). The study was to look for the possibility to improve and/or prevent the end cracking issue during FCB welding, center blind-hole drilling technique was used to measure the welding residual stress for five different cases, considering hot tearing mechanism, its influence factors and the relevant reported prevention measures. Unpredictable result was observed subsequently that transverse compressive stress is found on the shallow surface of weld seams, which could give supplementary information to the common assumption for conventional low heat input welding method that cracks initiation is caused by tensile stresses across the welded joints. The study concluded that FCB welding end cracking issue is caused by the comprehensive function of different stresses, and also properly use tack welding practice, suitable elastic run-off plate and relatively low heat input energy which will reduce the end cracking susceptibility for the tested materials.
[1] CB/Z 278, One-side submerged arc welding process with multiple wires for FCB (In Chinese), (2011).

[2] Yasuhisa Okumoto and Osamu Baba: Improvement of Flux-Copper Backing Welding Quality [J], Journal of Ship Production, Vol. 19, No. 4 (November 2003), pp.223-229.
[3] Tang Muyao, Rui Shuxiang, Xin Dingqian: Study on End Cracking during One-side Submerged Arc Welding, Transactions of the China Welding Instituion, Vol. 7, No. 3 (September 1986), pp.123-132.
DOI: 10.1080/09507118709451094
[4] E L Makarov , H Herold , M Schtraitenberg & A Pshennikov: Preventing hot cracking in end sections of long welds in one-sided, multi-arc, submerged-arc welding, Welding International, Vol. 14, No. 4 (2002), pp.305-309.
DOI: 10.1080/09507110009549184
[5] Okuda, N.: Studies on Generation Mechanism and the Prevention for End Cracking of One Side Automatic Welding Joint, report of Japan Welding Society, welding metallurgy workshop (In Japanese, 1978).
[6] IACS Unified Requirement W11, International Association of Classification Society Ltd. (2013).
[7] Rao Yizhong: Solutions to end cracking issue for FCB weld seams, Academic Conference on Energy conversation and pollution reduction in Shipbuilding Industry, Academic Committee for Naval Architecture, China's Society of Naval Architecture and Marine Engineering (In Chinese), pp.128-132 (2009).
[8] Bengt Akesson and Lennart Larlsson: Prevention of Hot Cracking of Butt Welds in Steel Panels by Controlled Additional Heating of the Panels, Paper D, PhD Thesis, Division of Solid Mechanics, Chalmers University of Technology, Gothenburg, Sweden (November 1973, August 1974, and March 1976).
[9] Zhang Wenyue: Fundamental of Welding Metallurgy, China Machine Press (In Chinese), pp.227-229 (1999).
[10] Dieter Radaj: Heat effects of welding; temperature field, residual stress, distortion. Xiong Dijing etc., Beijing: China Machine Press (In Chinese), pp.210-212 (1992).

DOI: 10.1007/978-3-642-48640-1_3
Submerged Welding The Mechanic Machine
[11] T Koseki: Solidification and solidification structure control of weld metals, Welding International, Vol. 16, No. 5, pp.347-365 (2002).
DOI: 10.1080/09507110209549544
.jpg/220px-Chamber_for_Welding_Fumes_(8743403735).jpg)
[12] Cui, Zhong Qi: Metallography and Heat Treatment, Harbin Institute of Technology (In Chinese), pp.296-297 (2000).
[13] Kou S: Welding Metallurgy, Second edition, Publ Wiley-Interscience Corp. pp.285-295 (2002).
Submerged Welding The Mechanic Training
[14] S Katayama: Solidification phenomena of weld metals (1st report). Characteristic solidification morphologies, microstructures and solidification theory, Welding International, Vol. 14, No. 12, pp.939-951 (2000).
Submerged Arc Welding Wire
DOI: 10.1080/09507110009549297
[15] S Katayama: Solidification phenomena of weld metals. Solidification cracking mechanism and cracking susceptibility (3rd report), Welding International, Vol. 15, No. 8, pp.627-636 (2001).
DOI: 10.1080/09507110109549415
[16] Kenji Shinozaki , Yamamoto Motomichi , Wen Peng & Tamura Tomoko: Prediction of occurrence of solidification cracking in weld metal [J], Welding International, Vol. 24, No. 12, pp.942-948 (2010).
Lincoln Submerged Arc Welding Guide
DOI: 10.1080/09507111003655325
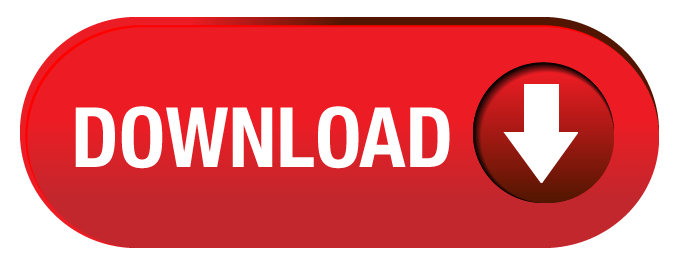